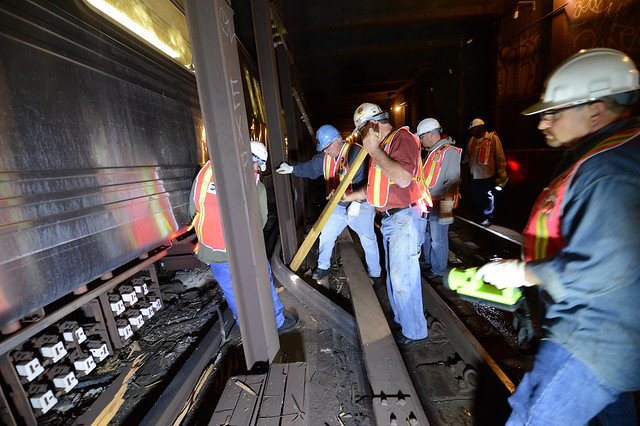
MTA crews inspect a derailed F train. A report on the May incident highlighted track-inspection deficiencies. (Photo: Marc A. Hermann / MTA New York City Transit)
Laid end-to-end, the tracks of the New York City subway system total more than enough to extend to Chicago. Every day, over 8000 subway trains pass through these tracks, and the system never shuts down. Thus, it’s a challenge for the MTA to keep everything in working order, and it requires diligence and an attention to detail to ensure nothing that could cause injuries or cost passenger lives is amiss. In May, that process broke down, and now the MTA is seeking to hold four workers accountable.
As you may recall, back in May, a Manhattan-bound F train derailed in Queens, snarling train traffic through the area for a few days. While no one was seriously injured, a fully train had to be evacuated, and it was the MTA’s first major subway derailment in some time. (The MTA’s derailment rate remains well below national average.) Still, the agency, as it should, takes these investigations seriously, and on Friday, Transit released a report fingering deficiencies in the track-inspection process. Four workers, the agency, said, will be disciplined for their failures.
“Nothing is more important than providing the safest transportation possible for our customers and employees, so determining the cause of this derailment was a top priority for us,” New York City Transit President Carmen Bianco said in a statement. “We immediately took corrective action to ensure we always focus on identifying and correcting track defects. This will minimize the risk of future derailments.”
The full report is available here as a PDF. The essence of it is that a series of minor defects that should have been caught by track inspection personnel and subsequently corrected were missed. The train operator, signal system, rolling stock and rail manufacturers were deemed to escape responsibility for the incident, but three Maintenance Supervisors and a Track Inspector are in the MTA’s crosshairs.
Here’s how the MTA summarized the findings:
New York City Transit’s Office of System Safety reviewed video data from prior automated inspections where the derailment occurred. The videos showed that a metal plate and fasteners under the rail had been broken for at least one year before the derailment but were not replaced. The wooden tie under that plate was also in poor condition. Maintenance records also showed that in the eleven months before the derailment, two other broken rails had been reported and replaced in the same 19-foot, 6-inch section of rail.
The combination of the broken plate, broken fasteners and deteriorated tie should have been prioritized for repairs. The report concludes that Division of Track personnel did not identify, document and correct the track defect at that location, either during regular inspections or when the two prior broken rails were replaced. They also did not adequately investigate the underlying causes of the broken rails.
Additionally, the report found that the top of the rail that broke was installed with a 1/8-inch vertical mismatch where the new rail met the slightly worn existing rail. In addition, the metal joint bars used to fasten the two rails together were reused, and one of them had a sharp edge where the top of the joint bar met the underside of the rail head. In addition, one of the six bolts required to secure the joint bar was not present.
To address these issues, the MTA has instituted new procedures regarding broken rails. This includes replacing broken plates and fasteners as soon as possible, and personnel will spend more time inspecting corridors with the highest number of broken rails. The agency will deploy ultrasonic inspection cars, and Division of Track is working to replace bolted joints with continuously welded rail. This should also allow trains to run faster through these corridors. All in all, it’s hard work to inspect hundreds of miles of underground track with trains constantly running over them, but as the MTA is keen to admit, that’s ultimately no excuse.
27 comments
Disciplining a few employees won’t solve the underlying causes of low motivation and lack of expertise. Using only sticks and no carrots means that problems will come up again and again. We need to move away from the journeyman/apprentice method and towards teaching industry best practices; away from exclusively punishments and towards incentives, both monetary and non-monetary; away from reacting to incidents and towards continuous improvement. These are basic organizational practices that have been standard in the private sector for decades.
Agreed. Personal accountability is important, but this seems far more like a systemic failure. Was the area identified as higher risk? If there is a pattern of rail breakage, who is analyzing that data and prioritizing more frequent inspections? If the time constraints are really tight, what are better ways to inspect these things continuously?
I don’t know how the MTA works internally, but from the outside they seem 40 years behind the times. We’ve known that blameless post mortems and root cause analysis was better than this kind of report for 20+ years now. Maybe these 4 guys actually screwed up, but rail inspection seems like something that will inherently have some missed problems. The system needs to account for that.
One of the recommendations in the report, echoing recommendations of the earlier Metro-North derailment report, is for the MTA to create a unified computerized tracking system that can identify areas of higher risk, patterns, locations to prioritize, etc. This is not something available today.
This system is possible. We’re working on drafting the requirements and the gap assessments for this system. The individual operating agencies will need to adopt systems or systems to allow information to transfer between groups. Currently, they information is siloed because of the Transit culture.
Not selling my blog here, but I think the solution is more than just a technology system. More info here:
http://tmblr.co/ZU10vl1Y4qRJ9
Which is precisely why the MTA needs to be “reinvented”. But inspite of the recommendations by the Reinvention Commssion, it will never happen because the MTA refuses to admit it has major organizational problems. That is evident just by going to the MTA website where the refer to the Commission’s draft report which is entitled “MTA Reinvention” but the MTA refers to the report as ” Transportation Reinvention” because they do not believe any reinvention of the MTA is necessary.
Even some of the people involved in the commission admitted to me that the MTA Reinvention Commission and subsequent report was a sham. There’s nothing in the final report to suggest forward progress, let alone reinvention.
That’s the most telling part of all this. As someone with a psych backround, I can tell you that in order for a person to get help they need to admit that a problem exists. It may appear obvious, but the MTA hasn’t reached that stage yet.
NYC Subway has already had serious problems in the track & structure maintenance department in particular, including falsified logbooks. This makes me unsuprised to discover more problems in the same department. Not clear what to do about it, though; it’s hard to fix a broken department even if *top management* recognizes the problem, because the lower-downs don’t recognize that it’s a problem. Too many rank-and-file maintenance workers’ reaction to the falsified logbooks was “oh, that’s totally reasonable, why are you complaining”.
Well, in the private sector, normally you apply motivational strategies: goal setting theory, foot-in-the-door, expectancy theory, motivational job designs. I think that last one might actually help a lot because a lot of MTA jobs seem repetitive to me.
Either that or you just fire everyone and hope to select better candidates. People tend to overestimate how easy that is, even in the private sector, but maybe some organizational cultures are just that poisoned.
Yeah. I don’t think NYC Subway culture is that poisoned; it should be fixable. They do get stuff done, and the motormen and ticket-booth agents and so on still seem to have a certain amount of pride in their work.
LIRR might be that poisoned, what with the fraud popping up practically everywhere you look.
There are much worse, of course. I can think of several examples of completely toxic organizational cultures at the federal level. The Central Intelligence Agency is very definitely that poisoned. So is the Drug Enforcement Administration. Both of them perform no actual useful function and should be liquidated entirely. Arguably, the culture is just as poisoned at the US Army, which is still being operated as if it’s World War II, complete with World War II-era paperwork. We’d probably have to start a new Army if we got rid of the existing one, though. The CIA and DEA could just be abolished, they’re not doing anything useful right now.
I haven’t taken a close enough look at the report yet, but I tend to agree with you.
The point I am making though is not whether the report did what it supposed to have done but how the MTA changed the title of the report because they don’t like the idea of them needing to be reinvented. That is because they do not believe they are doing anything incorrectly. They believe they are doing the best possible job within their budget conststraints. I wish that were the case. The sad fact is that while there are many good things that can be said about how the MTA operates and the job they do, there are also some very bad things that could be said about the agency. The MTA needs to recognize what their faults are and what they need to change. That push has to come from the outside, because it never will come from within.
The 947 different stakeholder/advocacy groups never have anything to say other than the trains and stations are dirty?
I hope they don’t reinvent, because if they do it will probably be into a monstrosity. They need reforms that other people have figured out already, not an NIH laboratory experiment led by the likes of Enrique Penalosa the pugnacious Straphangers.
And the best way to do that is by speaking to the employees and riders who know the system the best. Not by bringing in supposed experts who never rode an NYC train or bus.
This is some tin-foil-hat level hooha you’re spewing, Al. Did you read the report? Have you delved into the politics behind the commission? Did you attend the sessions where those employees and riders who know the system (ha. ha. ha. at the concept of that btw) spoke for hours about the same old same old? And do you really think most of the people on the panel weren’t intimately familiar with the system? The whole process was a joke, but you’re barking up the wrong tree here with regards to your criticism.
The riders will tell you they want better, more reliable service.
The employees will tell you they more or less the status quo.
You can’t satisfy both. We need outsiders, but the right outsiders.
The employees will tell you they want the status quo, but the worst employees will tell you they want the status quo with extra featherbedding and graft (and there’s already a hell of a lot at the LIRR).
There’s gotta be some way to change the employee culture. Some departments seem more motivated to provide good service than others.
“We need to move away from the journeyman/apprentice method and towards teaching industry best practices; away from exclusively punishments and towards incentives, both monetary and non-monetary; away from reacting to incidents and towards continuous improvement. ”
This is a unionized, civil service environment. Be happy for what you’ve got. The idea that anyone could be held accountable for anything is better than one would expect.
There are a few other questions. How old was that section of track. On what schedule is track replaced, and what is the average age? From whom was that plate and tie bought? Just a lemon, or are there more like them from the same order?
The MTA has wide latitude on how it educates its employees. But, since in the unions people tend to go up through the ranks, today’s younger employees are often stuck learning from people who worked during the era of the worst conditions of the system, where nitpicking over rules was not an option. They simply may not know current industry practices. And even if union rules require former workers to be the teachers, these teachers can still be given quality instructional materials, which is not what’s happening.
Many of your questions are answered in the report, which quite frankly I’m surprised was allowed to go public.
Perhaps I’m more tolerant of current practices at NYCT.
Because I compare them with the past, the LIRR, MetroNorth, the Department of Education, etc. etc. Makes the subway look pretty good.
Without the Lucius Pitkin reports and the correspondence with LPI the MTA report is a political statement.
In addition, the metal joint bars used to fasten the two rails together were reused, and one of them had a sharp edge where the top of the joint bar met the underside of the rail head. In addition, one of the six bolts required to secure the joint bar was not present.
Here’s where the question of ‘why?’ comes into play. Did they simply fail to bring enough replacement bolts or parts, were they lazy and possible lost some of the parts near the site and couldn’t be bothered to look for them, or were they trying to save a few $$$ by reusing what they had or leaving a bolt out here and there?
You omit another very distinct possibility: that for one reason or another they didn’t have the requisite new parts with them, so they reused parts and missed putting in one bolt due to time pressures.
There are many, many things to complain about the MTA, but safety is not one of them. There’ll always be mishaps, but I never think twice about boarding a train thinking that some accident could happen.
I think I understand what you’re really saying (“I never feel unsafe boarding a train”). But what you actually said (“The MTA does not have a problem with safety”) certainly appears to be plainly false at this point, as this particular derailment was explicitly caused by failure to properly perform maintenance, in a way specifically detrimental to passenger safety, and then lying/falsifying records about it.
That’s not exactly an “oops” situation. That’s a culture problem.
Sure, that’s because they appear to dumb everything down to
cover up foraccommodate multiple errors.Back in the day, trains on bolted rails could hit 60mph, which would come in handy on the Rockaway and Brighton Beach B trains. Now you can be on an express and watch a local completely pass by before it smacks its brakes for the next stop.
Could it be that mta are using the employees as scapegoats ( kimmel/ short at Pearl Harbor), covering their own ass deflecting the fact that the derailment was caused by them using cheap faulty Asian steel